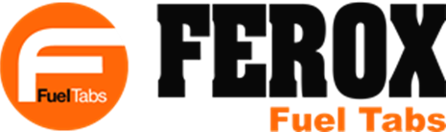
NEW TO AUSTRALIA
FUEL EFFICIENCY REDEFINED
FEROX allows you to use lower octane fuels
saving $$s on ongoing refuelling costs
COMBUSTION CATALYST
FEROX technology modifies surfaces in fuel particles and carbon deposits, achieving a
more complete burn of the fuel More energy
is extracted per drop, leading to an increase in efficiency and horsepower, improved fuel economy, reduced exhaust temperature,
and reduced harmful emissions. Also removes
and prevents carbon deposit build-up.
FUEL STABILISER
Stabilises fuel up to 12 months, maintaining
fuel quality for longer periods of time,
eliminating the need to drain fuel before
storage. This is achieved through the addition
of anti-oxidants that actively combat oxidation. Oxidation results in the formation of harmful particulates that can damage injection systems and clog filters.
CORROSION INHIBITOR
Corrosion can occur in the fuel tank and corresponding plumbing when water present in the fuel reacts with the metal to form rust. To prevent this, corrosion inhibiting compounds attach to the metal surfaces and form a protective barrier, preventing the effects of corrosive agents in the fuel tank and engine to reduce maintenance and increase longevity.
Ferox technology is based on the effects of the organic-metallic catalysts (multifunctional combustion catalysts) that modify the speed and temperature of combustion, and removes carbon deposits.
Ferox can be used with any type of liquid fuel from kerosene, petrol, diesel, LPG and in any application or engine type.
A typical engine develops a temperature curve that goes from 200°c in the cylinder walls to 1200°c in the center of the combustion chamber. Many components of fuel require a temperature higher than 600°c for optimum combustion. Ferox works by modifying the activation or combustion energy of the fuel molecules (catalytic effect), thereby accelerating and burning more fuel molecules at lower temperatures, as low as 200°c.
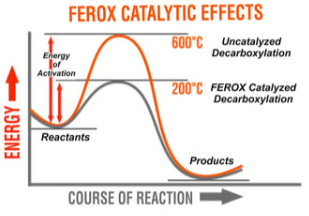
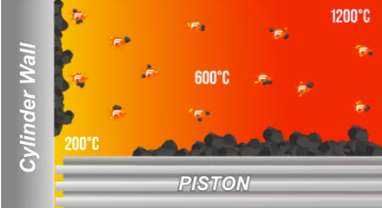
This allows a more complete combustion of the fuel, obtaining all its energy and the elimination of the carbon particles when exposed to a higher temperature, as well as the inhibition or increase of new carbon deposits. All this leads to lower emissions of CO, SOx, NOx, HC and PM10, decreased fuel consumption, improved performance, and lower maintenance costs.
The continuous use of this technology helps maintain the factory performance of the motor. Ferox protects the most critical engine parts such as valves, injectors and combustion chambers from harmful deposits.
HOW FEROX WORKS
Combustion is a chemical oxidation reaction, in which a large amount of energy is generally released. In all combustion there is a burning element (fuel) and an element that produces combustion (oxidising), usually gaseous oxygen.
The most common types of fuels are hydrocarbons. In a complete reaction, all the elements that make up the fuel are completely oxidised, forming byproducts such as carbon dioxide and water (CO2 and H20) that are the desirable compounds, sulfur oxides may occasionally appear SOx (if the fuel contains sulfur), and nitrogen oxides (NOx) depending on the temperature, amount of oxygen and pressure. (The complete and ideal gasoline reaction would be: C8H18 + 25O2 —
———> 16CO2 + 18H2O + Energy).
In incomplete combustion, the oxidiser and the fuel are not in the perect proportions as other compounds exist, or ideal conditions are not present, resulting in undesirable compounds such as carbon monoxide (CO) and carbon forming deposits (carbon and aromatic compounds in a state highly resistant to combustion).
These deposits are the source of many engine problems such as excessive fuel consumption, excessive harmful exhaust emissions, and high maintenance costs. Problems with fuel and incomplete combustion can eventually cause complete engine failure.
The formation of deposits begins with spherical molecules called primary particles, and branched aromatic chains, which are produced in the early stages of combustion. The various branched compounds are attracted to the primary particles, which rotate at extremely high velocity levels. When a branch is attached to a primary particle, the entire structure of the chain is rapidly wrapped around the primary particle and forms a secondary particle. These secondary particles agglomerate and form tertiary particles. This can occur when several primary particles join the same chain in different branches, and then simultaneously become a secondary and tertiary particle, since they wrap the chain. The tertiary particles agglomerate on the surface and re-coat to form quaternary particles, which form deposits. The surface structures of the chain of the deposits leave exposed branches. It is in these exposed branches where the FEROX begins to breakdown and destroy the deposits, modifying their surfaces.
The deposits are acidic and attract the oxide of the FEROX catalyst which is basic. When the two combine, an exothermic reaction occurs that releases a lot of energy, generating carbon dioxide and water (CO2 y H2O). The remaining compounds of this reaction have a low activation energy, easily decompose at high temperatures releasing a CO2 molecule and the catalyst oxide. This process is repeated and with time, the deposits are eliminated converting them into CO2 and water.
FEROX inhibits the formation of new deposits in the same way that it destroys existing deposits. It interacts with the ends of the aromatic chains and the binding sites in the primary particles, and this interaction prevents the primary particles from being wrapped in complete chains, blocking or destroying the binding sites and breaking the chains.
This interference prevents the process of agglomeration of deposits of primary and secondary particles, resulting in much lighter and smaller particles that do not adhere to each other, and oxidise more easily. The result of this is a decrease in particulate emissions, an increase in energy production, and a higher production of CO2 and water, which are the desirable end products of the combustion cycle.
EFFECTS OF FEROX ON THE COMBUSTION PROCESS
FEROX technology interacts with the longer and heavier chains, the temperature and speed that determines the combustion resistance of elements in the fuel and existing carbon deposits.
This interaction allows these deposits to break and burn.
The “molecular atomisation” of the fuel, the destruction and
burning of the surface of the deposits produces the following
positive effects in the combustion process:
More complete and standardised combustion
Reduces the requirements of excess air
Optimal use of available oxygen
Elimination of existing deposits
Better heat transfer
Lower fuel consumption
Greater efficiency in general
EFFECTS ON THE COMBUSTION BYPRODUCTS
FEROX improves the combustion process, which leads to the
following positive effects in combustion by products:
Elimination of old carbon deposits
Inhibition/Prevention of new formations of deposits
Decrease of:
fuel consumption
particles, smoke and soot
carbon content in the ash
NOX, SOX, CO y VOC emissions
cold corrosion due to the decreased SO3 formation
dirt and corrosion due to decrease the activity of V2O5
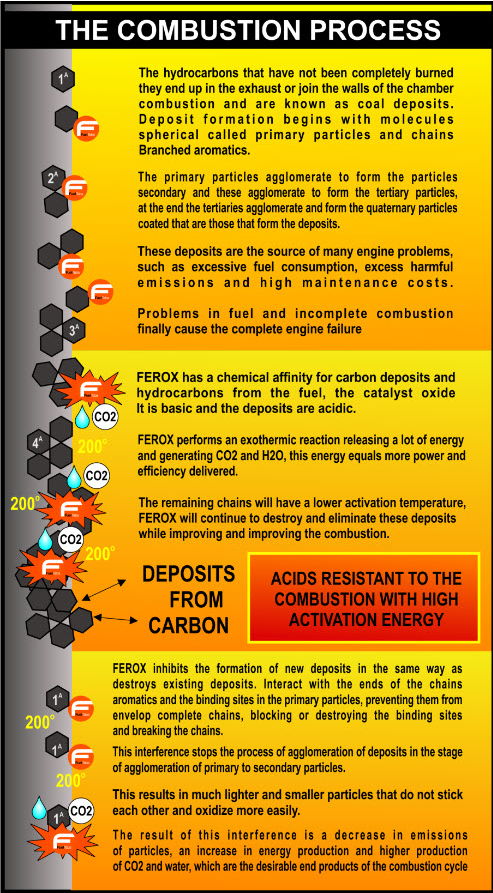